Revolutionizing the Automotive Industry: The Power of Automotive Plastic Molding
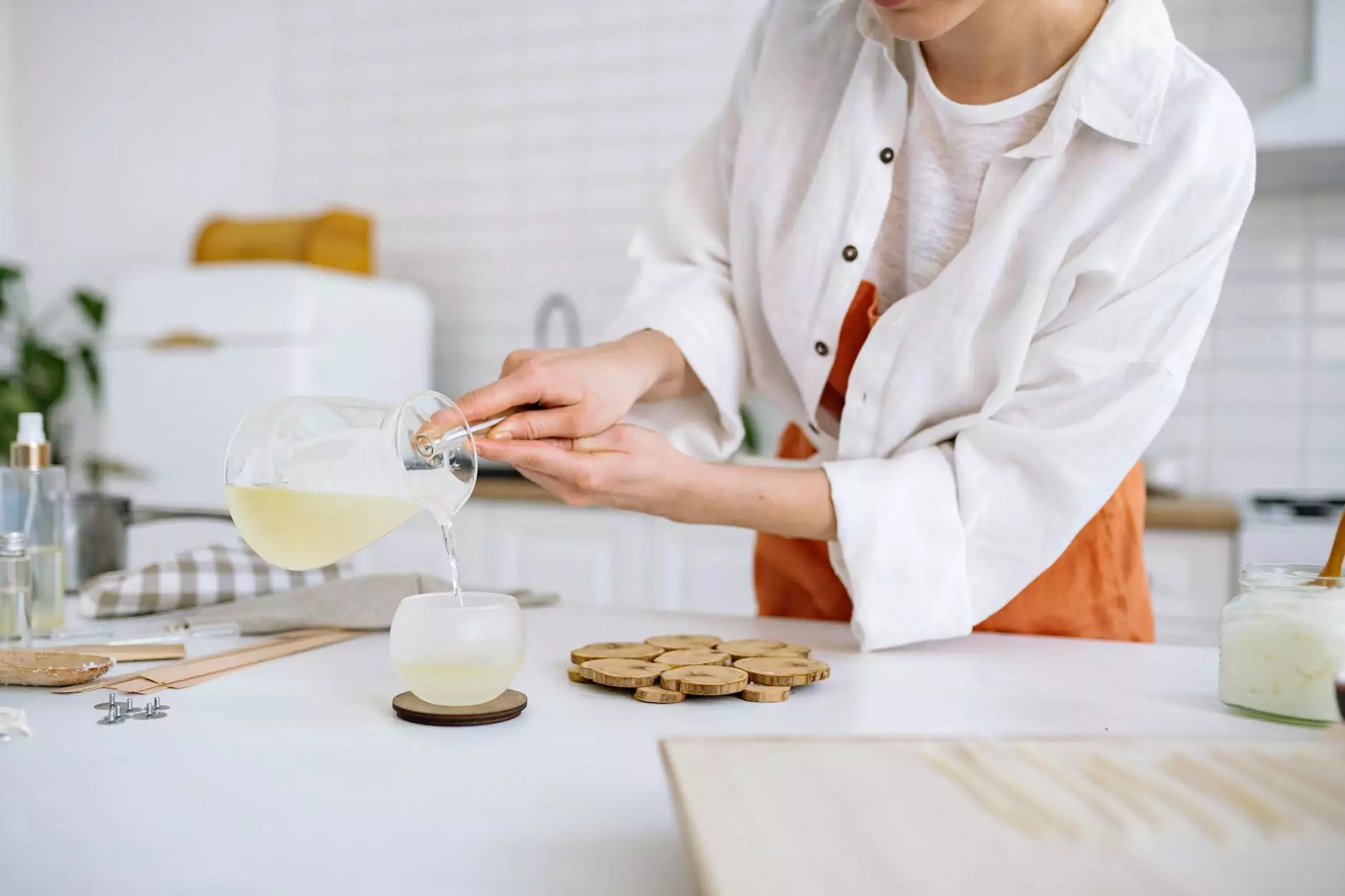
The automotive industry is undergoing a significant transformation, with innovations reshaping the way vehicles are designed and manufactured. One of the most impactful innovations has been the advent of automotive plastic molding. This technology is not just revolutionizing how vehicles are made; it’s also changing the way we think about materials, design, and sustainability in automotive manufacturing. In this detailed exploration, we will uncover everything you need to know about automotive plastic molding and its critical role in the automotive sector.
The Basics of Automotive Plastic Molding
Automotive plastic molding is a manufacturing process that involves shaping plastic materials into specific parts used in automobiles. This process is favored for its ability to produce lightweight, durable, and cost-effective components. Various molding methods can be utilized in this process, and the choice often depends on the desired application and part specifications.
Key Molding Techniques
- Injection Molding: This is the most common process where plastic is melted and injected into a mold.
- Blow Molding: Used for making hollow items by inflating heated plastic inside a mold.
- Rotational Molding: A process where plastic powder is heated in a mold, gradually coating the interior surface.
- Thermoforming: Heating a plastic sheet and forming it over a mold using vacuum or pressure.
Advantages of Automotive Plastic Molding
The benefits of utilizing automotive plastic molding in the manufacturing process are numerous and profound. Below are some key advantages:
1. Weight Reduction
One of the most compelling reasons for using plastic parts in automotive design is the weight savings they provide. Lightweight vehicles are more fuel-efficient, and by substituting metal with plastic in various automobile components, manufacturers can significantly lower the overall weight of a vehicle, enhancing performance and efficiency.
2. Cost Efficiency
Producing automotive parts through plastic molding can be cheaper than traditional metal fabrication due to lower material costs and reduced labor. Once the molds are created, the cost per part tends to decrease significantly with volume production, making plastic an economically viable choice.
3. Design Flexibility
Plastic parts can be molded into intricate shapes that would be challenging or impossible with metal. This allows automotive designers to innovate and create unique aesthetics while optimizing functionality. The ability to incorporate multiple features into one molded part reduces assembly time and costs.
4. Corrosion Resistance
Unlike metal, plastics do not rust or corrode. This durability ensures a longer lifespan for automotive components and contributes to the overall vehicle reliability, reducing maintenance costs over time.
5. Environmental Benefits
Advancements in recycling technology have allowed automotive plastic molding to align with sustainable practices. Many plastic materials can be recycled and repurposed, supporting a more eco-friendly approach to automotive manufacturing.
Applications of Automotive Plastic Molding
Automotive plastic molding finds utility in a myriad of applications within the vehicle. Here are some areas where this technology truly shines:
1. Interior Components
- Dashboards: Molded plastic dashboards provide a lightweight, design-friendly option for vehicle interiors.
- Door Panels: Plastic door panels not only reduce weight but also allow for complex designs and integrated features.
- Center Consoles: These can be easily designed to include storage solutions and controls.
2. Exterior Parts
- Bumpers: Many manufacturers use plastic in bumpers for impact resistance and to minimize weight.
- Fenders: Lightweight plastic fenders can enhance aerodynamics while providing protection.
- Grilles: Styling and functionality can be achieved with molded plastic grilles.
3. Under-the-Hood Applications
- Fluid Reservoirs: Plastic reservoirs offer corrosion resistance and weight savings compared to metal alternatives.
- Engine Covers: Plastic engine covers maintain aesthetics and functionality while reducing the engine weight.
- Air Intake Systems: Lightweight and flexible plastic designs can improve airflow and engine efficiency.
Challenges of Automotive Plastic Molding
While automotive plastic molding presents numerous advantages, there are challenges that manufacturers face in integrating these materials into their operations:
1. Material Selection
Choosing the right type of plastic for specific applications can be challenging due to the vast range of properties exhibited by different materials. Factors such as heat resistance, impact strength, and flexibility must be thoroughly considered to ensure the part’s reliability and longevity.
2. Manufacturing Complexities
Advanced molding processes can become intricate and require sophisticated machinery. This can present challenges in terms of production setup and operator training.
3. Recycling and Reusability
While many plastics can be recycled, the recycling process itself can be complex, and not all plastic components are designed with end-of-life recyclability in mind. This can lead to environmental concerns that manufacturers must navigate.
The Future of Automotive Plastic Molding
The future looks promising for automotive plastic molding. As technology progresses, so too does the complexity and capability of molding processes. Here are some trends shaping the future:
1. Advancements in Materials
The development of new, advanced materials will continue to enhance the capabilities of plastic molding in the automotive sector. Biodegradable plastics and composites will play a significant role in improving sustainability while offering superior performance.
2. Enhanced Manufacturing Technologies
Automation and integration of artificial intelligence in manufacturing processes enable more efficient production lines and better quality control. Technologies like 3D printing may also influence the customization of molded parts.
3. Increased Demand for Lightweight Vehicles
As environmental regulations tighten and consumer demands for fuel-efficient vehicles rise, the shift towards plastic components will likely accelerate. Automotive manufacturers will seek to balance performance, cost, and environmental impact, promoting the growth of automotive plastic molding.
Conclusion: Embracing Change in the Automotive Industry
The transition towards plastic materials in automotive manufacturing is more than just a trend; it’s a vital part of the industry's evolution. With the numerous benefits—*including weight reduction, cost efficiency, and environmental sustainability*—it is clear why automotive plastic molding is becoming increasingly popular. It is imperative for industry players to embrace this change, utilize advanced technologies, and innovate in ways that will define the future of mobility.
By investing in automotive plastic molding technologies, manufacturers like Deep Mould can ensure they stay ahead of the curve, producing high-quality products that meet the evolving demands of consumers and regulatory standards in the automotive landscape.