Understanding Plastic Injection Moulding Tolerances for Your Business
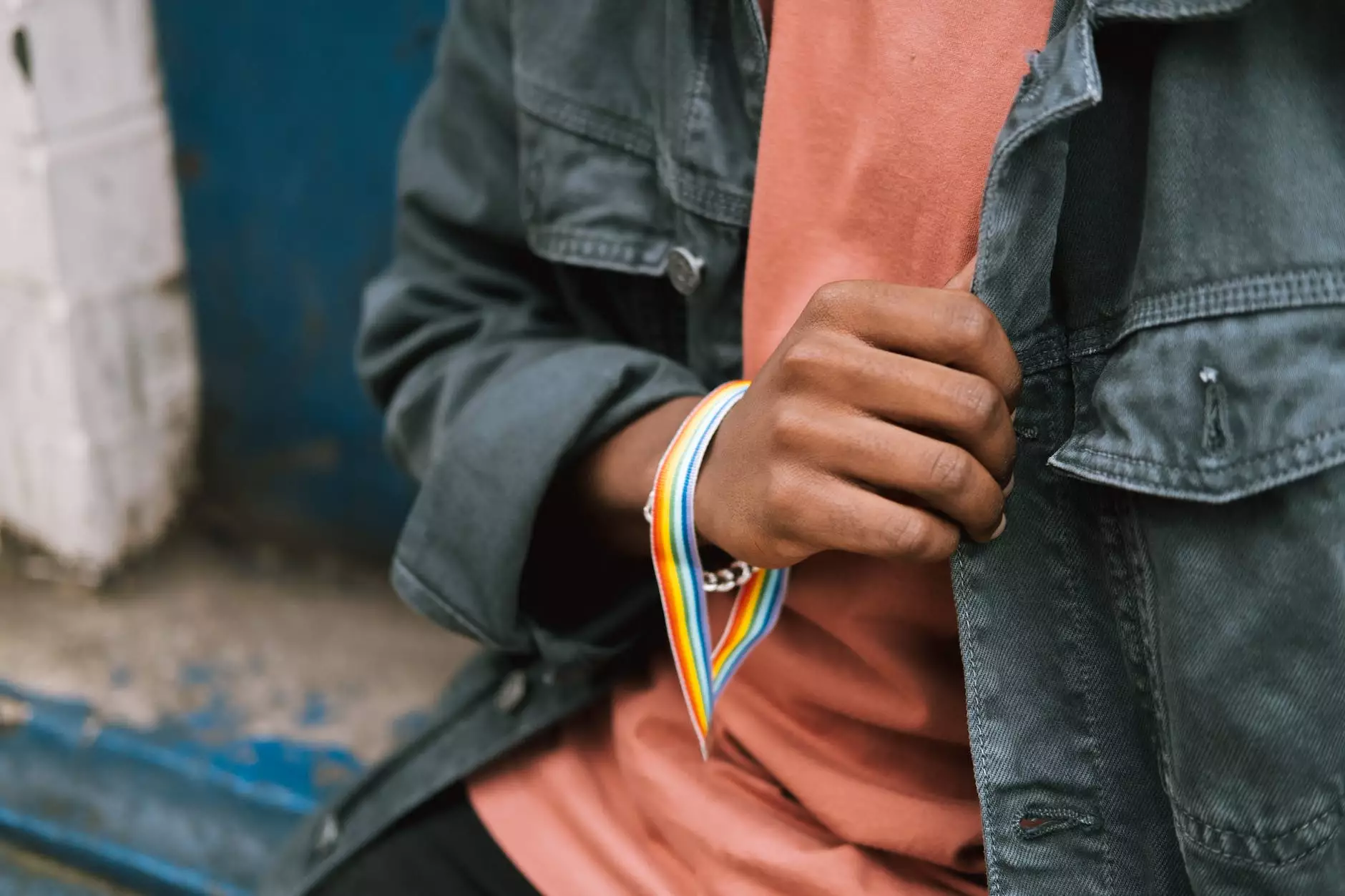
In the world of manufacturing, plastic injection moulding is a cornerstone technology that allows businesses to produce complex parts quickly and efficiently. However, the key to achieving high-quality output lies in understanding and managing plastic injection moulding tolerances. This article delves into the intricacies of tolerances, their significance, and how they influence the success of your manufacturing processes.
What Are Plastic Injection Moulding Tolerances?
Plastic injection moulding tolerances refer to the permissible levels of variation in the dimensions and performance of the molded parts. These tolerances are critical for ensuring that the final products meet the specifications required by designers and engineers. Tolerances can be categorized as:
- Dimensional Tolerances: These involve size specifications, such as length, width, and height.
- Geometrical Tolerances: These ensure the shape of the part conforms to design specifications.
- Assembly Tolerances: These define the acceptable limits for how parts fit together in an assembly line.
The Importance of Tolerances in Injection Moulding
The importance of understanding plastic injection moulding tolerances cannot be overstated. Here are several reasons why tolerances matter greatly in the injection moulding process:
1. Quality Assurance
With well-defined tolerances, manufacturers can maintain high quality in their production. Products that fall within tolerance limits ensure better functionality, leading to reduced returns and higher customer satisfaction.
2. Cost Management
Understanding the tolerances can greatly reduce production costs. By defining the right tolerances, companies can minimize material waste and avoid costs associated with reworking parts that didn’t meet quality standards.
3. Regulatory Compliance
Many industries are subject to strict regulatory standards. Understanding and implementing plastic injection moulding tolerances ensures compliance with these regulations, thereby avoiding legal issues and penalties.
4. Enhanced Performance
When tolerances are respected, the performance of components improves significantly. This is especially vital in industries where precision is crucial, such as automotive and aerospace manufacturing.
How to Determine Tolerances in Injection Moulding
Determining the appropriate plastic injection moulding tolerances for a specific project involves several critical factors:
1. Material Selection
Different materials have varying characteristics, which influence how they behave during the injection moulding process. For example, some plastics shrink more than others after cooling, necessitating tighter tolerances.
2. Part Design
The design of the part significantly affects the tolerances you can achieve. Complex designs may require tighter tolerances, while simpler shapes may allow for more leniency.
3. Mould Design
The quality of the mould also plays a crucial role in determining achievable tolerances. High-quality moulds can produce parts within much tighter tolerances than poorly constructed ones.
4. Environmental Factors
External factors such as temperature and humidity in the production environment can impact the material properties during moulding and therefore affect tolerances.
Setting Tolerances: Best Practices
To effectively set and manage plastic injection moulding tolerances, consider the following best practices:
- Consult with Engineers: Involve engineers early in the design phase to set realistic tolerances that can be achieved during production.
- Test and Validate: Conduct testing runs to assess whether the chosen tolerances can be achieved consistently.
- Use Advanced Technologies: Implementing modern technologies such as CAD and CAM can help in specifying and achieving tight tolerances.
The Impact of Poor Tolerances
Failing to control plastic injection moulding tolerances can lead to a myriad of issues:
1. Increased Production Costs
Parts that do not conform to set tolerances may need to be reworked or discarded, leading to increased production costs and wasted materials.
2. Product Failures
Products that fall outside of tolerable limits risk malfunctioning, leading to customer complaints and a damaged reputation.
3. Delays in Production
When tolerances are not managed well, production schedules may be disrupted as teams rectify the issues, causing missed deadlines and lost business opportunities.
Conclusion
Mastering plastic injection moulding tolerances is imperative for any business looking to excel in the manufacturing sector. By understanding, implementing, and controlling these tolerances, organizations can ensure high-quality outputs, minimize costs, and foster customer satisfaction. Investing time and resources into precision moulding not only enhances the quality of your products but also sets your business apart in the competitive landscape of manufacturing.
At Deep Mould, we are committed to delivering superior quality through meticulous attention to tolerances. Our experienced team can help your business navigate the complexities of plastic injection moulding, ensuring that your products meet the highest standards.
Contact Us
For more information on how we can assist your business in achieving optimal plastic injection moulding tolerances, please visit our website at deepmould.net or contact our customer service team today.