**Injection Molding at Home: A Comprehensive Guide**
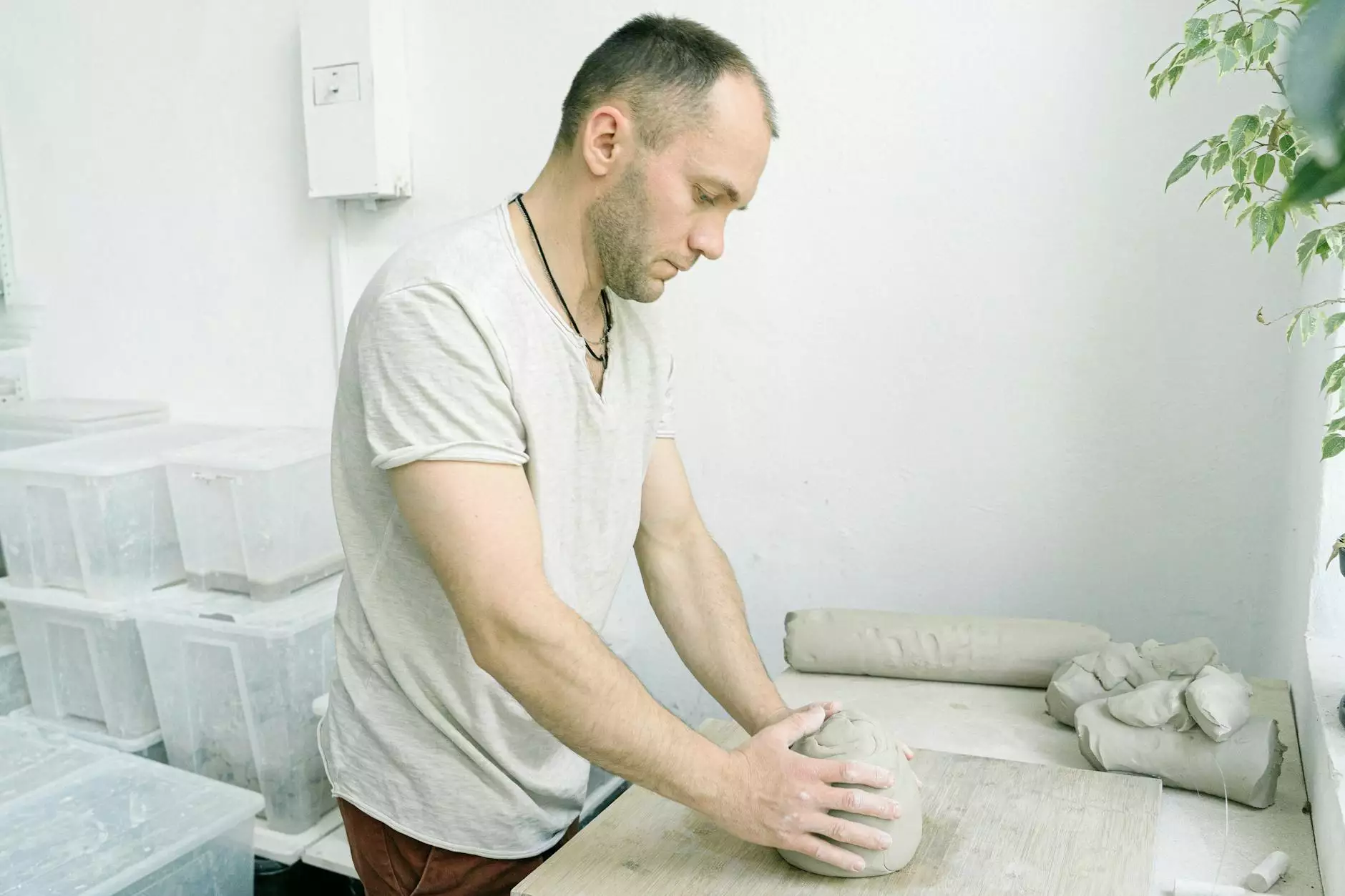
As technology continues to advance, the feasibility of injection molding at home has become an exciting prospect for hobbyists and small businesses alike. This technique, commonly used in industrial manufacturing, allows for the creation of precise, durable plastic parts. In this guide, we will explore the ins and outs of injection molding, focusing on how you can replicate this process in your very own home environment.
What is Injection Molding?
Injection molding is a manufacturing process for producing parts by injecting molten material into a mold. The process is widely used for the production of plastic components due to its ability to create complex shapes with high accuracy and repeatability.
The Benefits of Injection Molding at Home
There are many advantages to injection molding at home, including:
- Cost Efficiency: Lower initial setup costs compared to traditional manufacturing.
- Customization: Easily create bespoke parts tailored to personal or client specifications.
- Rapid Prototyping: Quickly test and iterate designs without significant delays.
- Small-Scale Production: Ideal for small businesses or hobbyists looking to produce limited runs.
- Quality Control: Greater oversight over the production process can lead to improved product quality.
Tools and Equipment Needed for Home Injection Molding
To get started with injection molding at home, you will need some essential tools and equipment:
1. Injection Molding Machine
A small-scale injection molding machine, often called a benchtop model, is essential for this process. These machines vary in size and cost but are compact enough for home use.
2. Molds
You will need to create or purchase molds specific to the parts you want to produce. Molds can be made from steel or aluminum, depending on your budget and desired production volume.
3. Plastic Resins
Select suitable thermoplastic resins for your project. Each type of resin has unique properties suited to different applications.
4. Safety Equipment
Don’t forget to invest in safety gear, including gloves, goggles, and a respirator, to protect yourself from plastic fumes and other hazards associated with the process.
Steps to Start Injection Molding at Home
Here’s a step-by-step guide to getting your home injection molding operation up and running:
Step 1: Design Your Parts
Use CAD software to create detailed designs of the parts you want to produce. This is crucial as the precision of your mold relies heavily on the accuracy of the design.
Step 2: Create the Mold
Based on your design, construct the mold. You can use CNC machines for high precision or manually carve out simpler molds. Make sure the mold is durable and capable of withstanding repeated use.
Step 3: Set Up Your Injection Molding Machine
Follow the manufacturer's guidelines to set up your benchtop injection molding machine. Ensure all components are assembled correctly and that you have a good understanding of its operation.
Step 4: Prepare the Plastic Resin
Heat the plastic resin to its melting point as indicated by the material's specifications. Be cautious during this step to avoid burns or other injuries.
Step 5: Inject the Resin into the Mold
Once the resin is melted, inject it into the mold using the injection molding machine. Make sure to follow the timing and pressure settings recommended for the specific resin you are using.
Step 6: Cool and Demold
Allow the part to cool and solidify within the mold. Once it has cooled sufficiently, carefully open the mold and remove your finished part.
Step 7: Finishing Touches
After demolding, you may need to trim excess material, sand rough edges, or add finishing touches depending on the intended use of the part.
Common Challenges When Molding at Home
While injection molding at home can be rewarding, it is not without its challenges. Here are some common issues and tips to overcome them:
1. Mold Misalignment
If your molds are not aligned correctly, you may produce parts that are misshaped. Always check the alignment before injecting the resin.
2. Air Traps
Air can get trapped in the mold, leading to defects in your parts. Design your mold with vents to allow air to escape during injection.
3. Inconsistent Injection Pressure
Variations in pressure can lead to weak spots or incomplete parts. Make sure your injection machine is calibrated correctly and that you maintain consistent parameters.
4. Material Selection
Choosing the right plastic resin is critical. Each type has a unique melting point, cooling time, and characteristics that affect the final product. Conduct thorough research and testing to select the best material.
Real-Life Applications of Home Injection Molding
The applications of injection molding at home are vast and varied. Here are some popular uses:
- Prototyping: Quickly create prototypes for product development.
- Custom Parts: Make specific parts for hobby projects, repairs, or replacement components.
- Art and Crafts: Produce unique items for handmade art and craft projects.
- Small Business Production: Create limited batches of products for small businesses or startups.
Conclusion: Embrace the Future of Home Manufacturing
Injection molding at home is an innovative way to explore your creativity and enhance your manufacturing capabilities. With the right tools, knowledge, and safety precautions, you can unlock a world of possibilities right in your garage or workshop.
Whether you're a hobbyist looking to make custom parts or a small business owner trying to control production costs, home injection molding is a pathway to achieving your goals. As equipment becomes more accessible and information more plentiful, there's never been a better time to dive into the world of plastic molding.
For high-quality molds and expert advice, consider partnering with experienced manufacturers like Hanking Mould, specializing in Plastic Mould Making and Plastic Injection Mould Manufacturing. Stay ahead of the curve, and embrace the potential of injection molding at home!